Within its first five years in operation, Madison, Wisconsin-based multifamily developer Neutral has planned more than 1,000 new units, raised over $100 million in development capital and set its sights on building the largest mass timber structures in the country — all while the CEO was in his early to mid-20s.
Nate Helbach co-founded Neutral with Matt Frazer, the company’s partner and chief technology officer, in 2019 with the goal of building multifamily housing differently, according to Helbach. What this meant was minimizing the carbon footprint of its projects and promoting health and wellness for residents — mainly with mass timber construction.
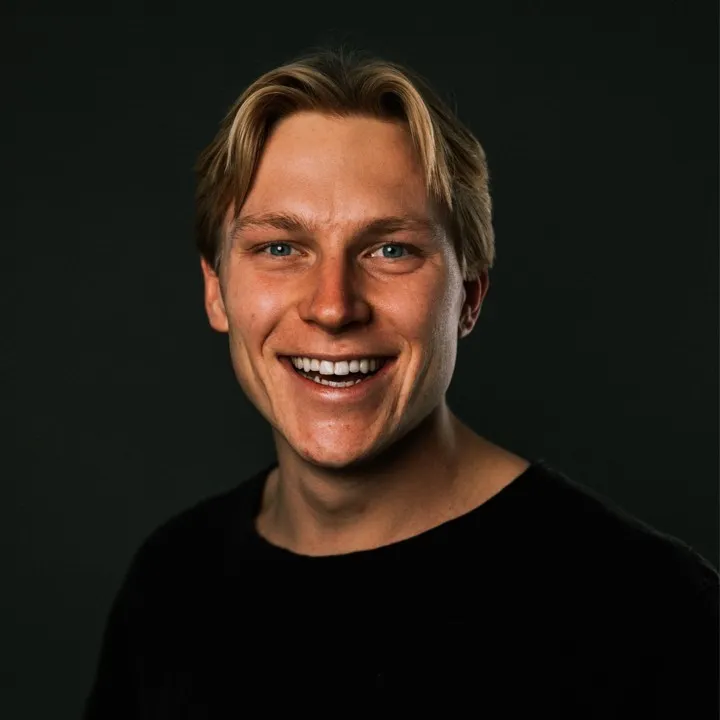
Today, Neutral is underway on multiple mass timber multifamily projects across the Midwest at both small and large scales. Among them is The Edison in Milwaukee, a 31-story mass timber tower that, when complete, will be the tallest in the U.S., according to Mihaela Cretu, a spokesperson for Neutral. Future plans include The Marcus Center, also in Milwaukee, which at 55 stories would be the tallest mass timber building in the world.
Here, Helbach talks with Multifamily Dive about why he focuses on mass timber, the impact of tariffs on his business and the future of mass timber in the industry.
This interview has been edited for brevity and clarity.
MULTIFAMILY DIVE: How did you decide to work in mass timber?
NATE HELBACH: We really looked at a plethora of different materials that we might be able to use for primary structural elements, and mostly you can only use steel and concrete in high-rise applications. But as of recently, with changes in the International Building Code, which is what we're governed by in the United States, we have been able now to use mass timber at a high-rise and mid-rise scale.
The reason why we chose mass timber is really going back to our core roots and main thesis around reducing carbon in the built environment, and it's really one of the only materials that you can use that has this ability to store carbon. When you put it into a building, it becomes a carbon sink. It’s led into this holistic wellness and longevity vision that we have for our tenants living in the building and really having a different experience.
How do your buildings promote health, wellness and longevity?
We do it in a few different ways. When we start construction, we're looking at embodied and operational carbon. We're looking at how to reduce embodied carbon, which is really all the carbon that comes from the different materials that you're using in your building, and then how to reduce operational carbon, which is more of how you design your building, and how much operational energy you're using during the actual operating period.
Early on in design, we're really looking at, how can we have better air quality? For example, inside, you're usually breathing 600 to 700 parts per million of carbon dioxide. Outside, if you're in a forest, you're breathing 350, sometimes lower. And in our buildings, you're breathing about 450, so we're bringing that down much closer to an outdoor atmosphere within the building that you're living in.
Neutral is reducing both embodied carbon and operational carbon in the building. Embodied carbon is reduced by using relatively more sustainable materials like mass timber, as well as pursuing local materials to reduce transportation impact. Operational carbon is reduced by using energy-efficient mechanical systems and passive systems like very high insulation and triple pane windows to reduce the need to heat or cool the building.
We have all of our water go through a reverse osmosis filtration system. We have gardens at all of our properties, and biophilic, natural materials throughout the space. And then for the more active participants of the wellness program, we actually have a clinical space on our larger sites where you can go and visit a doctor as a part of your lease, complimentary.
You get a full diagnostic, and that leads you into other different programs that we have that you have options to buy into. We have personal trainers and nutritionists on site at our larger properties that allow our tenants to pursue those different desires.
What markets are you most active in and why?
We're really active in Wisconsin right now, mainly because I'm from Wisconsin, so it was more out of coincidence. We do have an office in San Francisco, and we're expanding into the Bay Area, and so we're going to be starting projects there in 2026 and 2027. We are starting another project this year in the northwestern Arkansas region, in Fayetteville, and we see that as a big opportunity for growth with what Walmart is doing down there with their campus.
Cleveland Clinic just announced a $310 million hospital in Bentonville, Arkansas, and so we really see a big opportunity there for growth, and there's not a lot of multifamily developers. So we have a 40-unit project that's going to be starting this summer down there, and then we're hoping to find a few more opportunities to do some more projects in that area.
How has the current policy and tariff environment affected your operations?
It actually does not affect mass timber, interestingly enough, unless you're getting it from Canada. There has been a tariff on mass timber coming from Canada, but the mass timber we buy all comes from Europe. The nice thing about the tariff situation right now is because it's a reciprocal tariff, there has been no tariff that the European Union or Austria or Germany has charged on the United States importing mass timber from Austria and Germany. That is not necessarily out of the goodness of their heart, but more that we don't export any mass timber to Austria or Germany or the EU in general.
While short-term volatility can stir up the news cycle or shake the stock market, it hasn’t changed what we’re seeing on the ground. By adopting careful risk management practices at the outset of every project, using conservative financing, and procuring materials in advance, we position ourselves to navigate volatility and build long-term, sustainable value.
Our strategic mindset helps us be prepared for future uncertainty, but we’re also taking practical steps to reduce our exposure to tariffs. For projects still in planning or entering construction, we’re actively exploring domestic alternatives and continuing risk assessments for any imported components.
What is the future of mass timber in the multifamily sector?
I think it's a really big market opportunity for new multifamily developers and even lumber producers to start building panels and beams and columns to create that supply chain that we need to see. I think in the future, once we see that supply chain increase, then prices will come down a little bit further. It'll be really cost competitive with steel and concrete. Right now, it's about a 2%–4% increase from steel and concrete.
Once we see a wider adoption, there's a lot of other benefits. We save between 10% to 20% on our schedule, because you're able to prefabricate these panels. All mechanical, electrical, plumbing, and fire protection penetrations are already prefabricated in the factory. So when the panel comes on site, it's ready to place. It’s a much more efficient system. It just right now has a little bit of a cost increase. And so that's why we're not seeing it as widely adopted.